Demo Casters Is equipped with Die Casting machines ranging from 80 Tonne Locking Force to 400 Tonne locking force. Apart from this we also have a strategic tie up for casting on 600 and 800 Ton machines. Our Battery of Machines includes, 80 Ton, 120 Ton, 150/180 Ton and 350/400 Ton machines, as well as 600 Ton and 800 Ton machines. The machines are from some of the best machine manufacturers from Switzerland, Germany, Japan and Taiwan.
Our capabilities of casting are for parts ranging from 2.6 grams upto 5.5 Kgs, cast part weights.
All the machines are PLC controlled with many cutting edge features like, opening and closing dampening valves, which protect the tools from damage due to jerks and shocks, TFI ( Turbulence Free Injection ) systems or Parashot, which eliminated any kind of turbulence, air pick up or jerking in the injection stage of molten metal, which results in better, porosity free castings with enhanced surface and mechanical properties. Also the machines have a capability of storing over 300-500 preset die settings for each product to enable fool proofing.
We also have fully automatic robotic machines which are unmanned right from the metal loading into the furnace by trolley, to auto inject and die spray, followed by auto extract by robot and up to final casting delivered via conveyor.
Electrical and HSD Fuel Fired furnaces are used for melting and holding the alloy. These are world class equipments with temperature variations of as less as 1 degree. The furnaces are thyrister controlled and are extremely energy efficient. Only Silicon Carbide crucibles are used in the furnaces , so that no contamination or iron pick up occurs in the molten bath.
Special lubricants and water based release agents (polymer film type) are used by us to enhance surface finish and aid in smooth and clean casting processes. Also special high grade fluxes are used for dross removal and cleaning the molten baths to give us the best possible final metal specifications
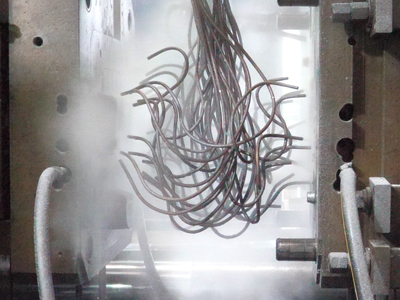
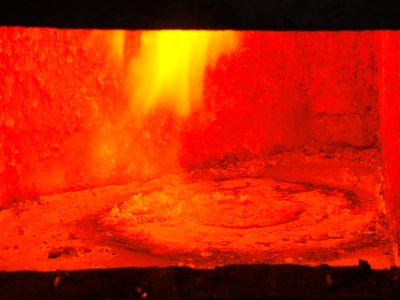

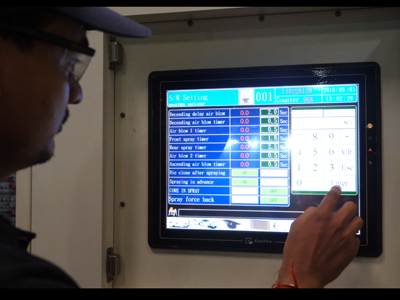
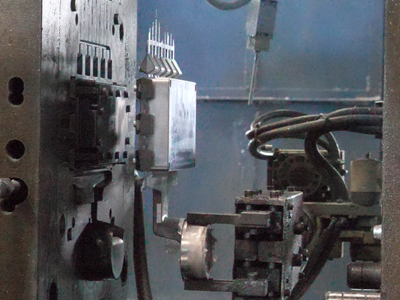
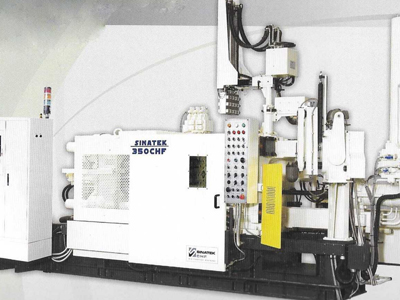
Recent Comments